light is right,通用是怎么削减车重的?
2016/5/24 雅斯顿
本文是雅斯顿的原创分享文章,来自撰稿人晓林。
从高压缩比到启停系统的配合,乃至更高级的混合动力,都可以看出车企在降低油耗的路上所付出的努力。伴随着消费观念越发成熟,汽车轻量化也正在受到消费者的认同。
实验证明,在确保性能的基础上,汽车重量每降低1%,油耗可降低0.7%,或者每减少100千克,百公里油耗降低0.3到0.6升。
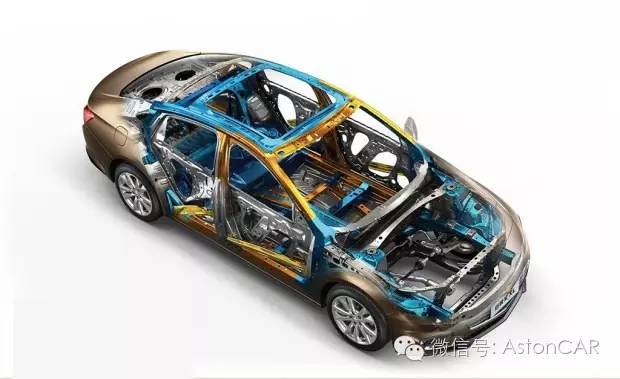
除了降低油耗,轻量化还可带来操控性、安全性方面的提升,并且为汽车内饰腾留更多的空间。相比其它效果单一的节油技术,轻量化拥有更广泛的实际用途。
近日,通用的能源中心负责人Charles Klein表示,为了追求效率最大化,每一克的车身减重对整个产品体系都有着重要意义。近年来通用推出的一系列新车,比起车身重量都有明显降低:比如新款科鲁兹减重113千克,别克君越减重136千克,迈锐宝减重136千克等等。又比如在北美市场作为全尺寸车型的凯迪拉克CT6,其车身重量比中大车型的宝马5系还要轻。

那么致力于轻量化的通用,有哪些技术亮点?
钢铝焊接技术
谈到轻量化,我们也许会先想到全铝车身。用铝代替传统的钢铁来制造汽车,刚度能提高60%,焊点能减少40%,车身重量降低30%到40%,对车身稳定性,碰撞安全性,节能减排等起到明显作用。
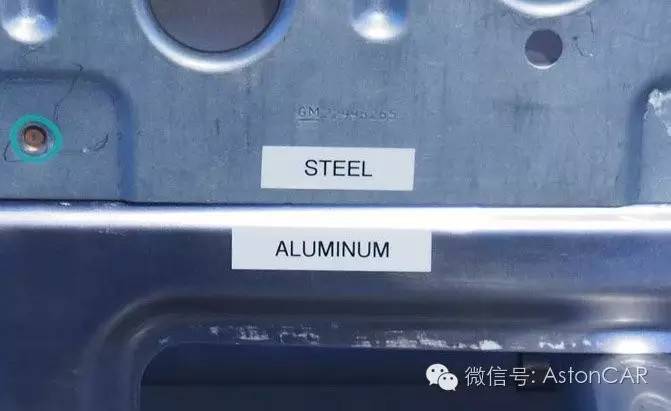
虽然全铝车身的减重效果出色,但铝板件材料成本较高,是普通钢板的3到6倍,而且制造工艺更复杂。高成本是技术发展的最大阻碍,这也是为什么全铝车身多采用在福特、奥迪、路虎、奔驰等品牌的高端车型上。
以福特为例,全铝车身的F-150作为技术的先锋者,实现了大规模的量产,带动了整个行业的发展。但福特为此付出了高昂的代价,从制造工艺的改变,到生产线的改造,再到工厂人员的培训,大刀阔斧的改革意味着每一环都需要大量投入,光是密歇根州的生产线拆除和建造就花费了数百万美元。

有没有一种方法,既能在新车上采用更多的铝材料,而又不需要将现有的生产线推倒重来?通用最近在新款凯迪拉克CT6上测试一项新的焊接工艺,将钢和铝焊接在一起,主要是发动机罩和汽车尾部的连接。
钢铝焊接比铝铝焊接更加困难,因为两者的熔点不同,相差大约900摄氏度,当钢材还在微热阶段,铝材就已经融化了。再者铝材在空气中极易氧化,在金属表面形成一层薄薄的氧化层,为焊接带来困难。
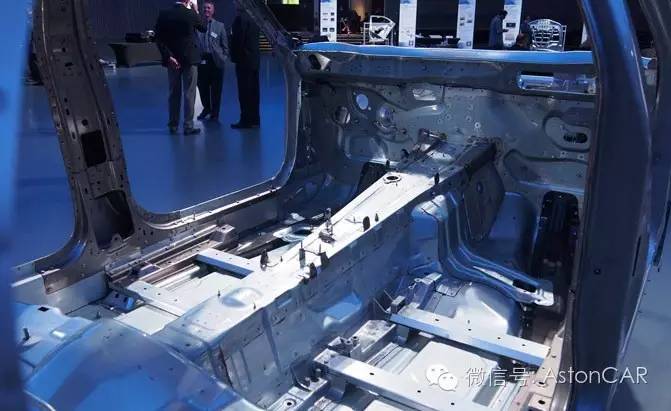
轻量化研究小组主管Blair Carlson表示:“从最初的想法到原型产品的测试,我们只用了两年时间,目前我们掌握了19项专利。”目前通用的焊装车间采用铝电阻点焊、铝激光钎焊、自攻螺接、自冲铆接四种工艺实现钢铝连接,其中铝电阻点焊就能解决铝材的氧化层问题。
和福特不同,通用希望更高效地利用现有的生产线,采用成本更低的方式来推动铝合金的使用。
镁合金注射成型
除了铝合金以外,通用也计划扩大镁合金零部件在汽车上的应用。由于镁的密度约为铝的三分之二,因此如果汽车采用镁合金,重量还能再减轻30%,同时镁合金还拥有吸震性强、铸造性能好、切割性能好等优点,目前大部分以压铸件的形式应用到汽车上。

通用目前在很多部件上都采用了镁合金,例如车门内饰板、发动机安装支架、车身板件、后尾箱内板等,减重效果出众。镁合金在很多方面都优于钢材和铝合金,但也有强度不高、抗腐蚀性和抗高温性较差的缺点,而且成本比铝合金还要高。
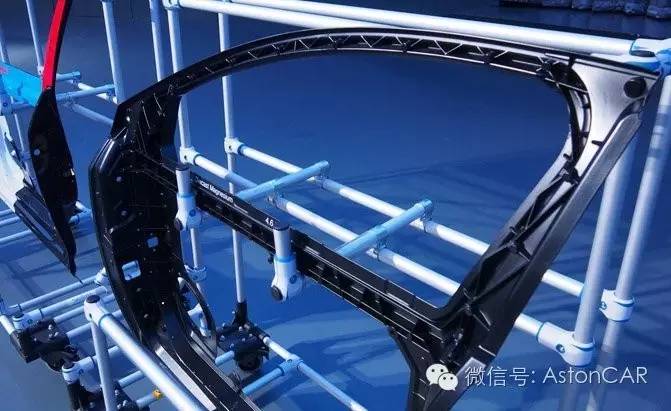
而在最近,通用又在研究镁合金的注射成型。轻量化实验室主管 Anil Sachdev带领他的团队,成功用注射成型技术制造出一整块镁合金车门。和传统的车门相比,镁合金车门的结构更简单,拥有不错的刚性,而且惊人的是重量降低了50%。
另一方面,压铸件需要在450摄氏度的环境下以非常慢的过程进行冲压成型,而用注射成型技术制造模型框架时,工序更容易快速,循环时间仅90秒。“对于汽车制造商而言,每缩减一秒的生产时间都能带来更高的经济效益。” Sachdev表示,“不过这项技术尚在研发阶段,我们不确定何时会推向市场。”
CAE结构优化设计
铝合金和镁合金的使用会带来明显的轻量化效果,但目前较高的制造成本,让这些材料无缘于大部分低端车型。不过轻量化并非只有材料一途,还可以从车身结构的设计优化入手。
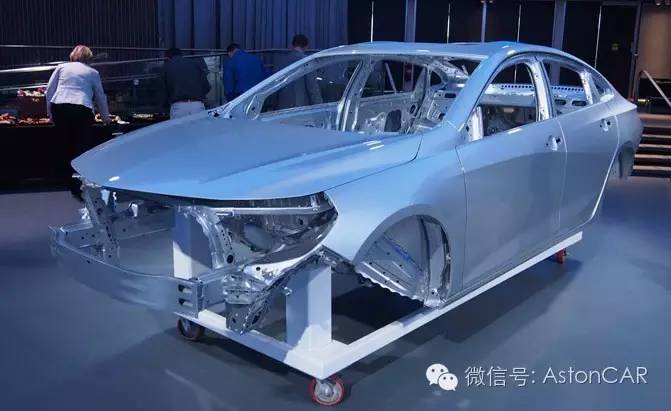
车身结构的设计优化,要使用一种名叫CAE(计算机辅助工程)的工具。简单地说,就是用计算机虚拟一辆汽车,其每一个零部件的数据都与实车一致。工程师们用它来进行虚拟碰撞测试,看看哪些地方刚性不足,需要加强材料,哪些地方是不重要的,可以去掉。
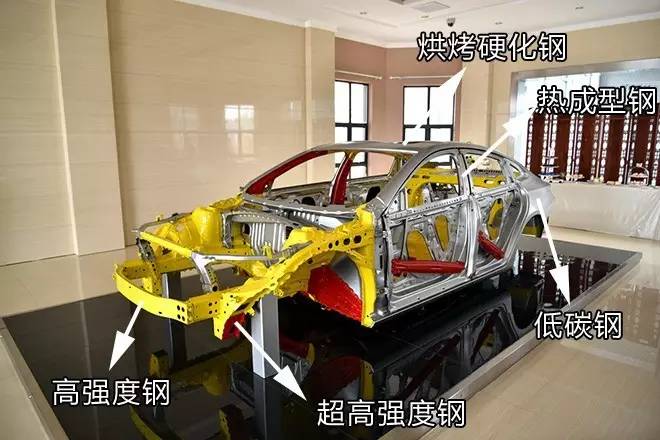
以迈锐宝XL为例,它的车身并没有采用铝制材料,而是采用超高强度钢。经过1000万个CPU小时的模拟测试,工程师们对车身前部进行重新设计,对发动机舱和车门连接处进行加强,在发动机盖和下摆臂上挖减重孔等等。经过设计优化,整车减重了120千克。

http://www.duyihua.cn
返回 雅斯顿 返回首页 返回百拇医药